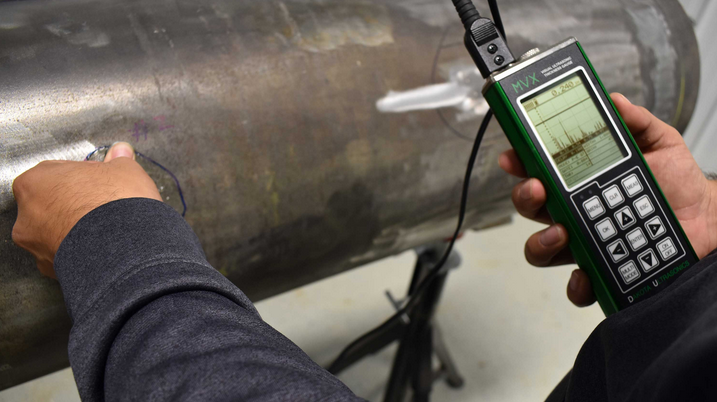
Ultrasonic thickness measurement and ultrasonic & magnetic particle inspection of welded joints
1. Ultrasonic testing (UT) is a non-destructive testing method that uses sound waves to detect cracks and defects in fabrics and materials. This method can be used to determine the thickness of a material, for example when measuring the wall thickness of a pipe. Thanks to the mobility of equipment and the availability of various methods, ultrasonic testing allows the inspection of large, irregularly shaped or non-transportable parts. Ultrasonic testing relies on electronic transducers that transmit high-frequency sound waves to materials. These sound waves demonstrate the fundamental properties of the material, giving it a crystal clear appearance. Images created by ultrasonic testing can show cracks, weld grooves and cracks, as well as show material thickness and describe moving components. Because this method has a higher power potential than other types of nondestructive testing, ultrasound can provide a clearer image than other types of nondestructive testing. other methods can show features that are deeper than the surface level. Depending on the testing requirements, parts can be tested by immersion (laboratory testing) or contact (handheld/airborne) testing. Ultrasonic testing is often used where radiographic testing is not possible because access to only one side of the test specimen is required.
Equipment:
2. Magnetic Particle Inspection, sometimes called MT, MPI or Magnetic Particle Inspection, is a non-destructive technique used to inspect surfaces and surface defects and defects. This process involves applying a magnetic field to the fabric and the fabric becomes magnetized. direct or indirect magnetization. This method uses a magnetic field and works best with ferrous metals such as nickel, iron, cobalt and some alloys. Magnetic particle testing is used to inspect components such as fixtures, rods, castings, bayonets, fasteners, welds and extrusions.
WET AND DRY CONTROL METHODS
Magnetic particle testing can be performed using dry or wet methods, depending on the application. In both methods, the product is charged with electricity to create a magnetic field. Iron particles are then applied to a portion of the dry or wet suspension. If there is a crack or other defect, particles will be attracted to the defect. Particles will accumulate around the leak and form an “indicator”. The indicator is assessed to determine its characteristics, cause and continuation. This allows you to understand the type and severity of any malfunction in the technical part of the element.
Delta ASM LLC CERTIFIED NON-DESTRUCTIVE TESTING EXPERTS
Our NDT inspectors are certified. By examining the nature of the surface, its location and size, highly trained and experienced inspectors can determine the source and cause of missing cuts both on and near surfaces. Our partnered, fully equipped NDT and Magnetic Particle Testing laboratories use state-of-the-art equipment to perform quality control on virtually every type of ferrous metal, component and assemblies.
Equipment: